A Análise de Causa Raiz ou RCA, em inglês, Root Cause Analysis, vem se tornando indispensável na manutenção industrial. E esta, por sua vez, tem cada vez mais necessidade de dirimir as ocorrências de falhas e não agir apenas no modo reativo.
Para ver mais conteúdos como esse, acesse nossos Cursos Certificados Vaportec.
Este modo normalmente deixa a equipe de manutenção sobrecarregada e sob pressão para rapidamente fazer a produção andar de novo, sempre “apagando incêndios”. Desta maneira, as despesas se tornam imprevisíveis e de grande valor.
Em sua conceituação, a RCA é definida como um processo conduzido exclusivamente por evidências. E que são manifestadas por causas desconhecidas ou não aparentes em não conformidade e que permitem melhorias contínuas. Quando não apresenta os resultados esperados, a RCA demonstra que não teve seu processo guiado por estas evidências.
6 passos do processo da análise de causa raiz
O processo de análise da RCA tem vários passos, que devem ser seguidos rigorosamente a fim de sanar as falhas. Abaixo, relacionamos os passos e explicamos cada um deles. Veja mais.
1 – Definição do problema
Normalmente, esse primeiro passo tem sua análise e solução dificultadas porque os participantes do grupo definem inúmeras falhas na mesma descrição, faltando objetividade. Para auxiliar nesta questão, fazer as perguntas certas, como qual é o problema, quando e onde aconteceu, qual meta foi prejudicada pelo problema e responde-las em poucas palavras vai permitir uma melhor definição da não conformidade.
Utilizado em situações mais complicadas, o conceito dos 5 Ps (partes, posição, pessoas, papel, paradigma) viabiliza uma ampla e dedicada análise para a definição das falhas.
2 – Caso necessário, realizar a análise de falhas
Essa análise é uma verificação minuciosa dos elementos não conformes e vai determinar o responsável pela falha. A relevância do como aconteceu é fundamental para a determinação da causa raiz no processo. São considerados cinco configurações que podem levar um elemento a falhar:
* sobrecarga (mecânica ou elétrica);
* fadiga;
* corrosão;
* falhas motivadas pela corrosão;
* desgaste.
3 – Identificação das possíveis causas
Uma versão simplificada do método de análise é a Árvore de Causas. Esse método, quantitativo e lógico, auxilia na identificação de combinações das falhas em elementos de um sistema ou nos equipamentos. Falhas humanas que podem causar acidentes e levam ao chamado evento principal. Para definir as raízes e permitir o melhor entendimento do evento, elas são divididas da seguinte maneira:
* raízes físicas (sobrecarga, fadiga, corrosão, desgaste);
* humanas (esquecimento, seleção errada, discriminação, erro de operação, cegueira situacional);
* raízes latentes ou organizacionais (falta de comprometimento dos colaboradores, intolerância da gerência, erros de comunicação, falta de processos e documentação técnica, falta de treinamento, especificações incompletas, incentivos e prioridades incorretos, falta de acesso à informação, uso de ferramentas erradas ou obsoletas).
4 – Verificação das causas concretas
Explicamos sobre isso e muito mais em nossos Cursos Vaportec.
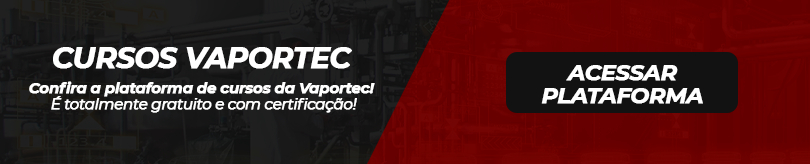
Após as análises iniciais, poderão ser rejeitadas as hipóteses que se confirmaram e por fim, ficarão somente as causas concretas do evento. Em se tratando dos equipamentos, este tipo de análise funciona como ferramenta de treinamento dos colaboradores da manutenção e até como uma direção para a correção de novos problemas que surgirem.
5 – Proposição da solução para o problema
Nesta fase são identificadas as soluções possíveis para cada não conformidade encontrada na fase anterior. Fundamental conferir de cada nova solução irá reprimir recorrências de erros e não causar novos. Devem ser levados em conta a facilidade de implantação e o investimento implicado nessas implantações.
6 – Implantação da solução e acompanhamento dos resultados
Para que todo o processo de análise realizado até esta etapa seja útil e efetivo, é imperativo a implementação das soluções apontadas. Para isso, é necessário elaborar um plano global contendo todas as ações e com prazos, responsáveis e recursos definidos para sua inserção, pois uma única ação corretamente estabelecida vale mais do que outras dez apenas previstas no plano ou implantadas erradamente.
Importante saber onde mais o problema encontrado poderia acontecer e se a solução encontrada também fosse possível de ser aplicada.
Conclusão
É preciso consciência do que se pode encontrar e estar preparado para transpor eventuais barreiras e resistências impostas pelas pessoas que dificultem a implementação da RCA.
Alguns pretextos mais utilizados por pessoas resistentes às mudanças, como o longo tempo do processo e seu custo. Ou como “moda” efêmera, muitas tentativas anteriores que não funcionaram…, tudo isso vem à tona quando há barreiras.
Porém, esses pretextos podem ser facilmente contrariados. Por exemplo, como o tempo consumido no processo de análise de causa raiz. Esse tempo certamente será menor do que o necessário para resolver problemas repetitivos e inesperados, sem falar nos recursos empregados.
Equipe Vaportec
Quer saber mais sobre conteúdos assim?
Temos diversos Cursos da Vaportec que podem ajudar você a crescer na sua carreira.
São profissionais experientes na área que montaram materiais de qualidade.
Clique aqui para se cadastrar nossa plataforma.
Aliás, você também pode continuar seus estudos lendo nosso e-book sobre Problemas Comuns: Meio, Material e Mercado.
Clique aqui para baixar, gratuitamente.
Estamos à disposição.
Um abraço,