As empresas que estão na dianteira quando falamos em tecnologia de ponta, processos eficientes e boas práticas de produção, sempre pensam em seus produtos a nível global. A concorrência está no mundo todo e a possibilidade de mercados distantes é uma realidade há muito tempo. É o que chamamos de globalização.
Para ver mais conteúdos como esse, acesse nossos Cursos Certificados Vaportec.
Para isso é necessário buscar a excelência em todos os níveis, inclusive na área da manutenção. É difícil imaginar uma empresa que alcance a excelência, se tornando referência mundial, praticando uma manutenção ineficaz.
Boas práticas em manutenção que não são praticadas
A diferença entre aquelas empresas que possuem níveis de excelência em manutenção e as que estão abaixo desse nível, é que as primeiras praticam as melhores práticas. Ou seja, o conhecimento normalmente está disponível para todos, porém a cultura da execução e melhoria contínua ainda é o grande desafio para grande maioria das indústrias.
O Brasil faz parte do segundo grupo, o que significa que para competirmos a níveis globais é precisa elevar a manutenção para a excelência. Esse patamar é a Manutenção de Classe Mundial.
O que temos quando não temos a excelência?
O resultado do baixo nível da área de manutenção nos dá o seguinte quadro:
- Alta taxa de retrabalho
- Falta de pessoal qualificado
- Problemas crônicos
- Falta de sobressalentes no estoques
- Número elevado de serviços não previstos
- Baixa produtividade
- Histórico de manutenção inexistente ou não confiável
- Falta de planejamento
- Abuso de “gambiarras”
- Excesso de horas extras
- Total falta de tempo para qualquer coisa
- Enfim, nada é medido, nada é estudado e em consequência nada é planejado.
Obtendo uma Manutenção de Classe Mundial
Explicamos sobre isso e muito mais em nossos Cursos Vaportec.
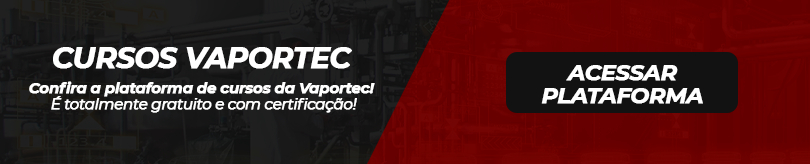
Na prática, se uma empresa quiser chegar ao nível de excelência mundial, terá que seguir os seguintes passos:
1- Planejar através de um Sistema de Gerenciamento – aqui a tecnologia tem grande papel. O uso de planilhas são de grande valia, porém um software específico para a manutenção trará todas as ferramentas de forma objetiva e simplificada, fazendo com que o gerenciamento seja mais natural e menos trabalhoso.
2- Trabalho em conjunto da operação manutenção – não é possível alcançar resultados excelentes quando se têm equipes trabalhando isoladas, cada um em sua bolha. É preciso integração nas atividades, sempre trocando informações entre operadores e o time de manutenção. Os problemas também devem ser avaliados e analisados em conjunto, pois a operação tem muito a agregar em termos de conhecimento prático.
3- Estoque de sobressalentes – é vital rever a política de estoque das peças sobressalentes tendo em mente o custo analisado de forma ampla, estratégica. O que afeta de forma crítica tem de estar presente no momento necessário. Além disso, é preciso um critério de maior qualidade na hora de escolher os fornecedores.
6- Tipos de manutenção adotadas – rever constantemente o uso dos tipos de manutenção. Privilegie a manutenção preditiva e detectiva. Isto porque o custo das manutenções corretivas e preventivas costumam ser maiores. A chamada Engenharia da Manutenção também tem papel importante nessa etapa. Busque mais conhecimento sobre como sua empresa pode utilizar esses recursos.
7- Treinamentos em polivalência – cada vez mais os problemas a serem resolvidos exigem mais conhecimento da equipe de manutenção. Isso porque refletem a complexidade das tecnologias modernas que integram os sistemas produtivos. Surge então a necessidade de os profissionais de manutenção tenham capacidades multidisciplinares e posturas mais flexíveis.
8- TPM – estudar e praticar os pilares da Manutenção Produtiva Total trará a base para uma cultura de excelência e focada em melhorias constantes.
9- Análises de Falhas – possuir mais de um recurso para análise das falhas. Para isso é preciso estudar, na prática, as ferramentas:
- FMEA – Failure Mode and Effect Analysis – Análise do Modo e Efeito da Falha;
- RCFA – Root Cause Failure Analysis – Análise da Causa Raiz da Falha;
- MASP – Método de Análise e Solução de Problemas;
- RCM – Reliability Centered Maintennce – Manutenção Centrada na Confiabilidade.
Lembre-se que a busca pela excelência é uma jornada. Para isso, busque todo o conhecimento disponível, fale com fornecedores experientes e mãos na massa!
Equipe Vaportec
Quer saber mais sobre conteúdos assim?
Temos diversos Cursos da Vaportec que podem ajudar você a crescer na sua carreira.
São profissionais experientes na área que montaram materiais de qualidade.
Clique aqui para se cadastrar nossa plataforma.
Aliás, você também pode continuar seus estudos lendo nosso e-book sobre Manutenção Industrial.
Clique aqui para baixar, gratuitamente.
Estamos à disposição.
Um abraço,