Uma válvula de segurança para vasos de pressão e caldeiras significa a diferença entre uma condição anormal de alta pressão sendo seguramente eliminada e a violenta ruptura do vaso. Mas então, o que isso quer dizer? Sua não utilização pode causar resultados catastróficos envolvendo morte, ferimentos pessoais e danos à propriedade.
Para ver mais conteúdos como esse, acesse nossos Cursos Certificados Vaportec.
A função de toda válvula de segurança para vasos de pressão, caldeiras ou processos industriais é aliviar o excesso de pressão devido ao aumento da pressão de operação acima de um limite pré-estabelecido no projeto do equipamento.
O objetivo ao instalar uma válvula de segurança é, sobretudo, a proteção de vidas e propriedades. Essa proteção ocorre quando a válvula é capaz de descarregar a quantidade exata de fluxo, suficiente para reduzir a pressão de um sistema a um nível seguro. Por isso, os termos “segurança”, “alívio”, e “alívio e segurança” se aplicam às válvulas que têm a finalidade de aliviar a pressão de um sistema.
História da válvula de segurança para vasos de pressão e caldeira
Esse tipo de dispositivo existe desde 1682 quando o francês Denis Papin o inventou. O modelo inventado funcionava com um sistema de contrapeso, ou seja, um peso ao ser movimentado ao longo de uma alavanca alterava a pressão de ajuste.
No começo da Revolução Industrial, quando o homem tentava compreender a energia e controlar o seu confinamento, ocorreram inúmeras baixas e grandes perdas materiais. Os primeiros geradores utilizados na indústria naval a vapor, por exemplo, explodiram 66 vezes consecutivas com várias vítimas. Naquela época, as tragédias diárias era frequentes devido às explosões de caldeiras para aquecimentos domésticos, inclusive, porque o controle dessas pressões era basicamente manual. Isso porque dependia operacionalmente do homem e, consequentemente, estava sujeito à falha humana.
Por isso, a partir de 1927, O Código ASME, Seção I, não permitiu mais que se instalassem válvulas de contrapeso em caldeiras.
Em 1848 o inglês Charles Ritchie foi o primeiro a introduzir um meio de aproveitar as forças expansivas do fluido para aumentar o curso de abertura do disco da válvula. Isso era uma espécie de lábio em volta da área de vedação do bocal, entretanto, fixo. Hoje, contudo, no lugar desse lábio, existe o anel do bocal, uma peça rosqueada usada para variar a força de abertura da válvula.
Em 1863 Willian Naylor introduziu mais uma melhoria para aumentar o curso de abertura da válvula, aumentando a força reativa. Essa melhoria era um segundo lábio em volta do disco, e que hoje em dia é uma saia na face inferior do disco.
Regras padrões para válvulas de segurança modernas
As válvulas modernas utilizam os princípios dos projetos anteriores para aproveitar as forças reativas e expansivas do fluido de processo para alcançarem o curso máximo e, assim, a vazão máxima.
Somente a partir de 1869 é que dois americanos, George Richardison e Edward H. Ashcroft, inventaram a válvula de segurança tipo mola. Entretanto, entre os anos de 1905 e 1911 houve na região da Nova Inglaterra, nos Estados Unidos, aproximadamente 1700 explosões de caldeiras e que resultou na morte de 1300 pessoas.
Assim, perto de 1908, alguns estados e municípios começaram a promulgar leis e ordens para regular a construção, instalação e operação de caldeiras e vasos de pressão. Contudo, os requisitos variavam enormemente. Então, logo a necessidade de um conjunto padrão de regras, aceitável a todos, fornecendo um razoável fator de segurança, tornou-se muito evidente.
Em função disso, em 1911, a ASME criou um comitê para formular tal conjunto de regras padrão. Dessa maneira, os primeiros frutos desse comitê apareceram em 1914, com a distribuição do Código de Caldeiras ASME, Seção I, para Vasos de Pressão Submetido a Fogo (caldeiras). Esta seção do código tornou-se uma exigência obrigatória em todos os estados dos Estados Unidos que reconheceram a necessidade por um regulamento. Foi publicada então em 1914 e formalmente adotada na primavera de 1915.
Tipo de válvulas de segurança e suas diferenças fundamentais
Explicamos sobre isso e muito mais em nossos Cursos Vaportec.
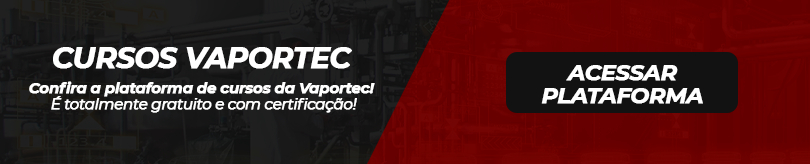
Válvula de segurança
É um dispositivo automático de alívio de pressão, atuada pela pressão estática na entrada e caracterizada pela abertura instantânea “POP” uma vez atingida a pressão de abertura.
* Usada para fluidos compressíveis: ar comprimido, vapor ou gás.
Válvula de alívio
É um dispositivo automático de alívio de pressão, atuada pela pressão estática na entrada. Assim, caracteriza-se por uma abertura progressiva e proporcional ao aumento de pressão acima da pressão de abertura.
* Usada para fluidos incompreensíveis: Líquidos.
Válvula de segurança e alívio
É um dispositivo de alívio de pressão adequado para trabalhar como válvula de segurança ou válvula de alívio, dependendo da aplicação desejada. Pode-se utilizar tanto para vapor, gás e líquidos, simultaneamente.
Termos comuns para válvula de segurança para vasos de pressão e caldeira
Pressão de projeto: é a pressão para qual se projetam as válvulas a fim de atender as condições de pressão e temperatura mais severas, previstas em operação normal
Pressão de operação: é a pressão efetiva atuante sob a válvula nas condições de trabalho.
Diferencial de alívio: (“Blow Down”): é a diferença entre a pressão de abertura e a de fechamento, expressa em porcentagem da pressão de abertura.
Pressão máxima de trabalho admissível (PMTA): é a máxima pressão manométrica de trabalho que se permite para o equipamento na temperatura, portanto, é compatível com o código de projeto, a resistência dos materiais, as dimensões do equipamento e seus parâmetros operacionais.
Nota: Ela é a base para o ajuste da pressão das válvulas de segurança que protegem o vaso.
Pressão de abertura – PA (“Set Pressure”): é a pressão manométrica na qual a válvula abre sob as condições normais de serviço.
Pressão de ajuste: é a pressão manométrica na qual a válvula abre em bancada de teste, incluindo correções para contrapressão e temperatura.
Estanqueidade: é o vazamento máximo admissível para as válvulas sob determinadas condições, seguindo parâmetros normativos.
Pressão de fechamento/reassentamento: é a pressão estática em que a válvula volta a fechar (o disco reassenta sobre o bocal), e não há fluxo mensurável.
Tensão ou pressão de alívio: é o resultado da soma das pressões de ajuste e a sobrepressão, medida na entrada da Válvula.
Pressão de vedação: pressão medida na entrada da válvula, logo após o seu fechamento, tendo vedação total.
Retirada de válvulas para manutenção
A válvula de segurança para vasos de pressão e caldeiras retirada de operação para manutenção deve ser testada em uma bancada de teste antes de ser desmontada para determinar a pressão de ajuste e a vedação. Esse procedimento é importante para uma eficiente manutenção, isso porque registram-se seus e depois os utilizam para uma possível ação corretiva.
Assim, o histórico da válvula, com suas características de entrada, demonstrando o real estado, se torna uma ferramenta importantíssima para definição da periodicidade ou os intervalos de manutenção.
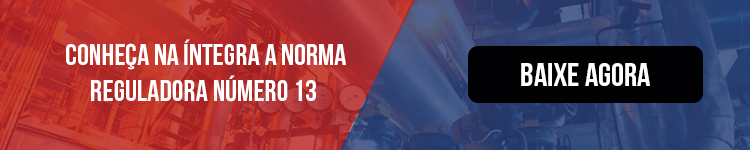
Sequência das atividades de manutenção para válvula segurança para vasos de pressão e caldeira
1) Receber e ensaiar as válvulas, efetuando registro dos ensaios realizados.
2) Registrar o estado real das válvulas através de inspeção visual, registrando em laudo e, de preferência, fotos.
3) Desmontar todos os componentes da válvula, analisando individualmente cada peça, relatando em laudo e, de preferência, com fotos.
4) Efetuar a recuperação dos componentes (quando necessário). Geralmente a sede e contra sede, quando danificadas, são necessárias a recuperação de suas faces com usinagem e lapidação apropriada. Quando a vedação é em elastômero, somente substituir o anel de vedação ou “o-ring”.
5) Efetuar substituição de peças, quando necessário (molas, vedações, parafusos, pinos, etc).
6) Montagem da válvula.
7) Levar para bancada de teste para efetuar os ajustes necessários, bem como sua calibração, observando as seguintes orientações:
- a) o fluido de teste deve ser ar comprimido ou nitrogênio;
- b) efetuar a regulagem da pressão de ajuste;
- c) verificar a repetibilidade da pressão de abertura da válvula;
- d) verificar a estanqueidade da válvula;
- e) verificar o aperto da contra porca do parafuso de ajuste da mola antes da instalação do capuz;
- f) inserir plaqueta de identificação;
- g) lacrar a válvula;
- h) emitir o Certificado de Calibração constando todos os dados dos ensaios realizados e, quando necessário, um relatório com os serviços executados.
Quer saber mais sobre conteúdos assim?
Temos diversos Cursos da Vaportec que podem ajudar você a crescer na sua carreira.
São profissionais experientes na área que montaram materiais de qualidade.
Clique aqui para se cadastrar nossa plataforma.
Aliás, você também pode continuar seus estudos lendo nosso e-book sobre Válvulas de segurança.
Clique aqui para baixar, gratuitamente.
Estamos à disposição.
Um abraço,