Você está por dentro das normas, procedimentos e equipamentos voltados para segurança com amônia na refrigeração industrial? Para quem trabalha na área é essencial ter conhecimento em soluções práticas, eficazes e, de fato, seguras paras as pessoas e equipamentos envolvidos nos processos de refrigeração.
Para ver mais conteúdos como esse, acesse nossos Cursos Certificados Vaportec.
Vazamentos de amônia, infelizmente, são mais comuns do que gostaríamos dentro da indústria brasileira. Por exemplo, a implosão de vasos de pressão, que são utilizados como reservatórios para este fluido refrigerante, é uma tragédia frequente no setor. Além disso, eventuais queimaduras de pele e acidentes ocasionados pela imprudência no momento do serviço, por parte de um profissional operador, manutentor ou prestador de serviços, são constantes, mas poderiam ser evitáveis.
Entretanto, antes de falar sobre a segurança e os equipamentos propriamente ditos, é necessário entender como que a amônia se tornou um fluido tão popular na refrigeração industrial.
Amônia: um gás refrigerante industrial
Em 1987 baniu-se o composto CFC em mais de 181 países, pois ficou comprovou-se que era 15 mil vezes mais nocivo para a camada de ozônio do que o próprio dióxido de carbono.
Conforme o Ministério do Trabalho e Emprego, a amônia apresenta uma série de vantagens, como o fato de ser o único agente refrigerante natural ecologicamente correto, por exemplo. Assim, seu nível de agressão à camada de ozônio é infinitamente menor, não agravando o efeito estufa.
Por isso, voltou-se a utilizar a amônia voltou em larga escala nos sistemas de refrigeração, principalmente nas atividades industriais que trabalham com alimentos perecíveis, como os armazéns frigoríficos, a indústria do pescado, as fábricas de gelo, os laticínios e a indústria de bebidas.
Em contrapartida, a amônia possui uma alta toxicidade e torna-se explosiva em concentrações de 15 a 30% em volume, o que requer cuidados específicos na sua utilização.
Nas instalações frigoríficas, especificamente, os fluídos refrigerantes possuem características físico-químicas especiais e em condições de temperatura, pressão e umidade diferenciadas do habitual. Dessa maneira, aumenta-se os riscos específicos à segurança e à saúde, relacionados com o tipo do agente refrigerante utilizado, assim como com as instalações e equipamentos.
Características da amônia
Mesmo considerando estes pontos, a amônia foi e é o gás mais popular quando falamos em indústria e refrigeração industrial no Brasil. Sendo assim, ela pode ser vista desde o armazenamento de frutas até o congelamento de carnes, passando pela climatização de salas em ambientes químicos e petroquímicos. A amônia tem seu uso industrial em todos os estados brasileiros, em variados mercados e também em diversos tamanhos de aplicações e plantas frigorificas.
Assim, a utilização da amônia nos sistemas industriais de refrigeração, se deve em função das suas características como agente refrigerante:
- – ser volátil ou capaz de se evaporar;
- – apresentar calor latente de vaporização elevado;
- – requerer o mínimo de potência para sua compressão à pressão de condensação;
- – apresentar temperatura crítica bem acima da temperatura de condensação;
- – ter pressões de evaporação e condensação razoáveis;
- – produzir o máximo possível de refrigeração para um dado volume de vapor;
- – ser estável, sem tendência a se decompor nas condições de funcionamento;
- – possibilitar que vazamentos sejam detectáveis por verificação simples;
- – ter um odor que revele a sua presença;
- – ter um custo razoável;
- – existir em abundância para seu emprego comercial.
Riscos na utilização da amônia na refrigeração industrial
Conforme a Norma Técnica 03/2004, que trata sobre a refrigeração industrial por amônia, esse fluido apresenta um grau de risco moderado em relação a incêndios e explosões, quando exposta ao calor ou chama. No entanto, a presença de óleo e outros materiais combustíveis são outros fatores que aumentam o risco de incêndio.
Além disso, há também o risco à saúde do ser humano. O gás é um irritante poderoso das vias respiratórias, olhos e pele. Dessa forma, dependendo do tempo e do nível de exposição podem ocorrer efeitos que vão de irritações leves a severas lesões corporais. A inalação pode causar dificuldades respiratórias, broncoespasmo, queimadura da mucosa nasal, faringe e laringe, dor no peito e edema pulmonar.
A ingestão causa náusea, vômitos e inchação nos lábios, boca e laringe. Além disso, em contato com a pele, a amônia produz dor, eritema e vesiculação que, em altas concentrações, pode resultar em necrose dos tecidos e queimaduras profundas.
O contato com os olhos em baixas concentrações (10 ppm) resulta em irritação ocular e lacrimejamento. Mas em concentrações mais altas, pode causar conjuntivite, erosão na córnea e cegueira temporária ou permanente. Reações tardias podem acontecer como catarata, atrofia da retina e fibrose pulmonar.
Além disso, a exposição a concentrações acima de 2.500 ppm por aproximadamente 30 minutos pode ser fatal.
Amônia no setor frigorífico
Em relação às instalações frigoríficas, as maiores preocupações são os vazamentos com formação de nuvem tóxica de amônia e as explosões. Segundo a NT 03/2004, “as principais causas de acidentes são falhas no projeto do sistema e danos aos equipamentos provocados pelo calor, corrosão ou vibração”. Isso pode decorrer da manutenção inadequada ou, até mesmo, da falta dela no sistema ou em seus componentes, como em válvulas de alívio de pressão, compressores, condensadores, vasos de pressão, equipamentos de purga, evaporadores, tubulações, bombas e instrumentos em geral.
Entretanto, é importante observar que mesmo os sistemas com ótimos projetos podem apresentar vazamentos de amônia, se operados e/ou mantidos de forma precária. Causas mais frequentes de vazamentos:
- – abastecimento inadequado dos vasos;
- – falhas nas válvulas de alívio, tanto mecânicas quanto por ajuste inadequado da pressão;
- – danos provocados por impacto externo por equipamentos móveis, como empilhadeiras;
- – corrosão externa, mais rápida em condições de grande calor e umidade, especialmente nas porções de baixa pressão do sistema;
- – rachaduras internas de vasos que tendem a ocorrer nos/ou próximo aos pontos de solda;
- – aprisionamento de líquido nas tubulações, entre válvulas de fechamento;
- – excesso de líquido no compressor;
- – excesso de vibração no sistema, que pode levar a sua falência prematura.
Segurança com amônia na refrigeração industrial
Explicamos sobre isso e muito mais em nossos Cursos Vaportec.
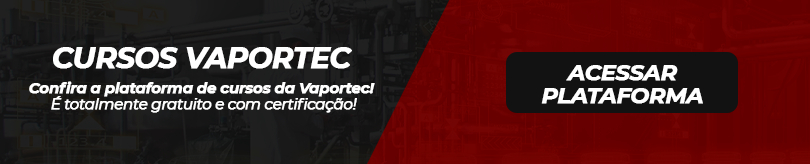
Segundo a 03/2004 para refrigeração industrial por amônia (MTE, 2005), uma instalação segura de amônia sustenta-se em três pilares: projeto apropriado, orientado por normas e códigos de engenharia; manutenção eficaz; e operação adequada.
Além disso, os elementos para a gestão da segurança e saúde em estabelecimentos que possuam esse tipo de sistemas devem incluir:
- – informações de segurança do processo;
- – análises dos riscos existentes;
- – procedimentos operacionais e de emergência;
- – capacitação de trabalhadores;
- – esquemas de manutenção preventiva;
- – mecanismos de gestão de mudanças e subcontratação;
- – auditorias periódicas;
- – investigação de incidentes.
Em relação à estrutura do local de operação, NT 03/2004 (MTE, 2005) também estabelece diretrizes distintas. A primeira dela refere-se ao local onde a casa de máquina é instalada, que deve ser no térreo, de preferência em edificação separada. Entretanto, em casos que isso não seja possível, deve-se instalar fora do prédio, com o máximo de paredes exteriores possível.
Uma boa ventilação é fundamental e, nos casos de ambientes fechados, o pé-direito deve ser, no mínimo, de 4 metros, existindo pelo menos duas saídas de emergência. Além disso, é essencial a existência de detectores de vazamento no local.
Inspeções e manutenções em instalações de amônia na refrigeração industrial
Além das observações acima, a norma técnica 03/2004 também recomenda uma inspeção visual em todos os pontos críticos como soldas, curvas, junções, selos mecânicos – pelo menos a cada 3 meses.
Tanques e reservatórios devem passar por inspeção de segurança completa, nos prazos máximos previstos na legislação (NR-13) que, assim recomendando-se radiografia de soldas e testes de pressão. Todas as etapas da manutenção do sistema devem ser cuidadosamente especificadas e adequadamente registradas, dessa maneira, definindo-se procedimentos específicos para operações de risco, tais como a purga de óleo do sistema, a drenagem de amônia e a realização de reparos em tubulações.
EPI’s e segurança dos operadores
As empresas devem possuir equipamentos básicos de segurança pessoal para cada trabalhador envolvido diretamente com a planta, dispostos em locais de fácil acesso e fora da sala de máquinas. Portanto, confira as exigências:
- – uma máscara panorâmica com filtro de amônia;
- – equipamento de respiração autônomo;
- – óculos de proteção ou protetor facial;
- – um par de luvas protetoras de borracha (PVC);
- – um par de botas protetoras de borracha (PVC);
- – uma capa impermeável de borracha e/ou calças e jaqueta de borracha.
A NT 03/2004 (MTE, 2005) também afirma que deve ser estabelecido por escrito o plano de emergência para ações em caso de vazamento, realizando-se treinamentos práticos, prevendo e disponibilizando mecanismos de comunicação da ocorrência, evacuação das áreas, remoção de quaisquer fontes de ignição, formas de redução das concentrações de amônia e procedimentos de contenção de vazamentos.
Em caso de vazamento com grande concentração de gases, faz-se necessária a utilização de máscaras autônomas e proteção total do corpo com tecido impermeável ou, na ausência dessas, o umedecimento dos trajes. Portanto, na mesma linha de raciocínio, deve-se aspergir água para forçar a reação de hidratação e formação do hidróxido de amônia.
É crítico que se observe que, na ocorrência do vazamento, a amônia, em estado aerossolizado, comporta-se como um gás denso. Em caso de fogo, recomenda-se o uso de água para resfriar recipientes expostos. Mas para fogo envolvendo amônia líquida, utiliza-se pó químico ou CO2.
Devem operar os sistemas de refrigeração por amônia devem, apenas profissionais qualificados, com certificado de treinamento, conforme o disposto na NR-13.
Os operadores devem ter conhecimentos completos sobre o sistema. Além disso, devem saber que partes do sistema requerem manutenção preventiva e como realizá-la de forma segura.
Equipamentos de segurança em sistemas de amônia na refrigeração industrial
Normalmente, as salas de máquina operam 24 horas por dia, 7 dias por semana, durante 365 dias, para garantir a produção em larga escala. Assim, é imprescindível mencionar alguns equipamentos quando o assunto é segurança em salas de máquinas. Sobretudo, equipamentos que utilizam amônia como fluido refrigerante, afinal, a segurança com amônia é essencial. Confira os principais:
- – pressostato para amônia;
- – transmissor de pressão para amônia;
- – manovacuômetro para amônia;
- – válvula de segurança para amônia;
- – chave de nível para amônia;
- – transmissor de nível para amônia;
- – detector de amônia.
Você pode conferir mais sobre cada um dos equipamentos em nosso texto “Segurança com amônia em sala de máquinas“. Entretanto, é importante ressaltar que todos os equipamentos sejam específicos para amônia. Assim, eles garantem maior segurança e confiabilidade ao sistema.
Equipamentos para amônia segundo a NT 03/2004
A NT 03/2004 (MTE, 2005) estabelece regras bem importantes sobre a utilização dos equipamentos usados em plantas de refrigeração por amônia.
Uma das principais refere-se ao dimensionamento dos mesmos e suas instalações. Assim, todos os equipamentos do sistema de refrigeração devem ser adequadamente dimensionados e instalados, além de testados antes de sua operação. Além disso, é essencial sinalizar e identificar os componentes, inclusive tubulações.
Sobre a armazenagem de amônia, ela deve ser feita, preferencialmente em área coberta, seca, ventilada, com piso impermeável e afastada de materiais incompatíveis, recomendando-se a instalação de diques de contenção. Portanto, é essencial que se definam cuidados especiais com os cilindros e tanques de amônia, inclusive no seu abastecimento.
Ainda possui alguma dúvida em relação à segurança com amônia do seu sistema? Está com dificuldade em suprir as demandas da sua planta e precisa melhorar o seu processo? Entre em contato conosco, teremos prazer em entender o seu sistema e projetar, juntos, as melhores soluções para a sua empresa.
Referência
Nota técnica nº 03/2004: refrigeração industrial por amônia : riscos, segurança e auditoria fiscal. – Brasília : MTE, SIT, DSST, 2005.
Quer saber mais sobre conteúdos assim?
Temos diversos Cursos da Vaportec que podem ajudar você a crescer na sua carreira.
São profissionais experientes na área que montaram materiais de qualidade.
Clique aqui para se cadastrar nossa plataforma.
Aliás, você também pode continuar seus estudos lendo nosso e-book sobre Segurança em Sistemas de Amônia.
Clique aqui para baixar, gratuitamente.
Estamos à disposição.
Um abraço,